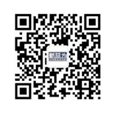
微信公眾號二維碼
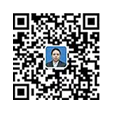
微信咨詢顧問二維碼
一、由顧客確定產品價值結構
1、產品價值結構的涵義。
新益為精益生產咨詢公司概述:產品價值結構是產品價值的構成、比例和價值過程,即產品所提供的各種收益、支出及其比例關系,以及價值實現(xiàn)的過程。
精益生產咨詢
產品價值結構是確定企業(yè)的某種產品為客戶提供的具體利益,以及每種利益的數量;還需要確定客戶購買產品的各項支出,各項支出的金額;收益和支出之間有什么樣的聯(lián)系;為了實現(xiàn)產品價值,各種收益和支出的過程是什么。
對于一般顧客,家樂福超市免費提供塑料袋,麥德龍的塑料袋是收費的。由此可見,家樂福為普通顧客提供了塑料袋的好處,而麥德龍卻沒有為普通顧客提供這種優(yōu)惠。原因是兩家商家的目標群體不同。家樂福主要面向普通客戶,麥德龍主要面向團體客戶。
2、產品價值結構由顧客確定 。
在當前信息經濟社會的背景下,由于高素質的人才、低成本的信息,先進的技術、成熟的管理模式、顧客的強勢購買力等等外部環(huán)境因素,企業(yè)已具有了經濟的滿足顧客多樣化需求的社會條件。
企業(yè)競爭的焦點是如何利用工業(yè)社會的規(guī)模優(yōu)勢和信息社會的信息低成本優(yōu)勢,來滿足顧客個性化的需求。這時候,產品的價值結構就由顧客來確定了。當然,社會經濟條件下,企業(yè)由于經濟性的約束,大部分情況是企業(yè)提供一個價值組成清單,在清單的范圍內,由顧客確定產品價值結構。
精益管理的出發(fā)點是產品價值結構,價值結構只能由最終顧客來確定,而價值結構也只有由具有特定價格、能在特定時間內滿足顧客需求的特定產品(商品或服務,而經常是既是商品又是服務的產品)來表達時才有意義。
二、變“成批移動”為“單件流動”
1、成批移動與單件流動的概念
成批移動就是在制品成批的在各工作地加工,并按工藝流程成批的經過各工作地移動。成批移動源于成批生產,成批生產是周期性的成批的輪番生產幾種產品。在成批生產條件下,生產具有重復性,產品品種較少,每種產品的產量較多,形成多品種周期性的輪番生產的特點。
單件流動就是在制品一件一件的按照工藝流程經過各工作地進行加工、并連續(xù)移動,即按照工作流程將作業(yè)場地、設備(作業(yè)臺)合理配置,一般劃分為幾個工作段,產品在每個工作段生產時,零件一個一個地經過各種工作地進行加工、移動,不是一批一批地加工、移動,每個工序最多只有一個在制品或成品。
在每個工作段中從生產開始到完成之前,沒有在制品放置場地及入箱包裝的作業(yè)。作業(yè)人員隨著在制品走,從作業(yè)區(qū)的第一個工序到最后一個工序都是該作業(yè)人員操作。
2、將“成批移動”變?yōu)?ldquo;單件流動”。
事實上如果產品按從原材料到成品的過程連續(xù)來生產的話,即單件流動,工作能更好、更有效地完成。在單件流動中,因為在每個工段中各工序銜接在一起,前工序做完一個在制品,就可立即“流”到下一工序繼續(xù)加工,所以工序間幾乎沒有搬運距離,也沒有在制品,因此在制品數量可以大幅度降低,生產空間也跟著減少了。
不良品一旦發(fā)生,就可立即發(fā)現(xiàn),而且很容易地確認出是由哪一臺機器、哪一個作業(yè)者做出來的。這有助于消除不良品。更重要的是生產周期大幅度縮短,更能滿足市場多變的需求。由于不必為每臺設備單獨設置人口存放處和出口存放處,場地也節(jié)省了許多。
三、生產由顧客拉動
1、推動式生產與拉動式生產。
推動式生產就是計劃部門根據市場需求,按產品構成清單對所需的零部件規(guī)格和數量進行計算,得出每種零部件的需要量和各生產階段的生產前置時間(Leadtime),確定每個零部件的投入產出計劃,按計劃發(fā)出生產和訂貨的指令。
在推動式生產中,每一生產車間都按計劃生產零部件,將實際完成情況反饋到生產計劃部門,并將加工完的零部件送到下一道工序或下游生產車間,無視下一道工序和下游生產車間當時是否需要。在此方式中物流和信息流基本上是分離的。整個過程相當于從前(前工序)向后(后工序)推動,故這種方式被稱為推動式(Push)方法。
拉動一詞最簡單的意思是,在下游顧客(或工序)提出要求之前,上游企業(yè)(或工序)不能進行產品生產或提供服務。
拉動式生產就是從市場需求出發(fā),由市場需求信息決定產品組裝,再由產品組裝拉動零部件加工。每道工序、每個車間都按照當時的需要向前一道工序、上游車間提出需求,發(fā)出工作指令;上游工序、車間完全按這些指令進行生產。
物流和信息流是結合在一起的。整個過程相當于從后(后工序)向前(前工序)拉動,故這種方式被稱為拉動式(Pull)方法。
2、生產由顧客需求拉動。
采用拉動式系統(tǒng)可以真正實現(xiàn)按需生產。如果每道工序都按下道工序的要求,在適當的時間,按需要的品種與數量生產,就不會發(fā)生不需要的零部件生產出來的情況。
一旦有了在顧客需要的時候就能設計、安排生產和制造出顧客真正需要的產品的能力,就意味著企業(yè)可以拋開銷售預測,直接按顧客的實際要求生產。這就是說,企業(yè)可以讓顧客按需求拉動產品生產,而不是把顧客常常不想要的產品硬推給顧客。
當顧客知道他們可以及時得到他們所要的東西時,而且,當生產者停止定期的減價銷售活動,不再把已經生產出來卻沒人要的產品推銷出去時,顧客的需求就變得穩(wěn)定得多了。
3、消除產業(yè)價值鏈的浪費
精益管理必須超出單個企業(yè)的范疇,去查看生產一個特定產品所必須的全部產業(yè)活動。這些活動包括從概念構思經過細節(jié)設計到實際可用的產品,從開始銷售經過接收訂單、計劃生產到送貨,以及從遠方生產的原材料到將產品交到顧客手中的全部活動。
形成精益企業(yè)確實需要用新的方法去思考企業(yè)與企業(yè)間的關系,需要一些簡單原則來規(guī)范企業(yè)間的行為,以及沿產業(yè)價值鏈的所有環(huán)節(jié)的改善。
(1)產業(yè)價值鏈的概念。
產業(yè)價值鏈是產業(yè)中從原材料到銷售的圍繞某種(或某類)產品的所有企業(yè)所形成的增值鏈,即從原材料的供應開始,經過價值鏈中不同企業(yè)的制造加工、組裝、分銷等過程直到最終用戶的一條價值鏈。物料在價值鏈上因加工、包裝、運輸等過程而增加其價值,給相關企業(yè)都帶來收益。
(2)消除產業(yè)價值鏈中的浪費。
在分析每個產品(或產品系列)的產業(yè)價值鏈時通常會暴露出大量的、錯綜復雜的mu—da。產業(yè)價值鏈中的浪費和企業(yè)中的浪費一樣,可以分為兩類:一是有很多活動雖然不創(chuàng)造價值,但是在現(xiàn)有技術與生產條件下是不可避免的,如為保證質量,焊接處要檢驗;乘飛機從青島到敦煌要到西安轉機的額外旅途(為一型浪費)。
二是還有很多不創(chuàng)造價值而且可以立即去掉的步驟(二型浪費)。實際上產業(yè)價值鏈的浪費是非常多的,常見的有以下幾種:
庫存的浪費。由于上游和下游企業(yè)之間沒有形成信息的共享,以及生產計劃的相對獨立,導致上游企業(yè)的產品不能夠及時的銷售出去,造成庫存的浪費。
過量加工余量的浪費。
價值鏈中的“成批”模式造成的過早、過量生產,以及由此帶來的庫存等浪費。
流通中的浪費。由于企業(yè)之間沒有形成良好的組合,造成流通環(huán)節(jié)的效率不高所帶的流通浪費。要實現(xiàn)精益管理,就要遵循消除產業(yè)價值鏈的浪費這一原則。
等待的浪費。就是由于在生產周期中的人員或機器等待而產生的浪費。如:等待原材料到位,等待維修人員到位,等待流程完成等等。實際上浪費在等待上的時間通常是可以避免的。有些等待時間無法避免,但是效率可以提高(例如,清洗、質量檢查、材料接收等)。
返工的浪費:是指由于流程的重復或修改而造成的浪費。比如反復的調整生產指標或參數直到達標為止;精益專家何守中強調返工未能滿足客戶規(guī)格的制成品都屬于返工浪費。
返工違反了“一次做對”的宗旨,其造成的因素可能是在作業(yè)方法、材料、機器或人力的不足。返工會造成需要預備額外的資源,以預防返工而造成生產中斷。
走動的浪費:人員或機器在流程內的不必要移動,比如在轉產過程中,操作人員走動去拿零件、工具,或者操作員在操作機器控制部件中的移動等。一般來說手動和機器的操作經常包括不必要的走動;不必要走動的原因也可能是工廠的布局尚未為不同的客戶需求進行優(yōu)化而造成的。
四、精益管理帶給企業(yè)的益處
對于制造型企業(yè)而言,在以下方面已經有無數的實踐證明是取得成效的:庫存大幅降低,生產周期減短,質量穩(wěn)定提高,各種資源(能源、空間、材料、人力)等的使用效率提高,各種浪費減少、生產成本下降,企業(yè)利潤增加。
同時,員工士氣、企業(yè)文化、領導力、生產技術都在實施中得到提升,最終增強了企業(yè)的競爭力。對于服務型企業(yè)而言,提升企業(yè)內部流程效率,做到對顧客需求的快速反應,可以縮短縮短從顧客需求產生到實現(xiàn)的過程時間,大大提高了顧客滿意度,從而穩(wěn)定和不斷擴展市場占有率。
五、中國企業(yè)的精益管理推行
推行精益管理模式,對于促進中國企業(yè)改革有非常重要的意義。
首先,精益管理有利于實現(xiàn)兩個根本性轉變。一方面精益管理的出發(fā)點就是強調顧客確定價值和顧客拉動,而市場經濟的基本動力是用戶的需求,另一方面,粗放型與集約型最本質的區(qū)別在于是否最大限度地減少各種形式的浪費,合理利用社會資源,提高國民經濟的整體效益。
其次,精益營理有利于企業(yè)運行模式的改革。在國有企業(yè)中,浪費現(xiàn)象嚴重,產品開發(fā)周期長,成功率低,生產過程庫存過大,物資積壓,造成資金沉淀。運用精益管理方法,將有助于企業(yè)改革原有運行模式,消除浪費,使之運轉起來。
第三,精益管理有利于企業(yè)集團的戰(zhàn)略實施,發(fā)展企業(yè)集團是國有企業(yè)改革的一個重要戰(zhàn)略,企業(yè)集團往往由處在生產過程上、中、下游的一組企業(yè)形成,如果在企業(yè)集團中運用精益管理,則使每一個企業(yè)之間相互協(xié)作關系更和諧、更緊密,使每個企業(yè)都減少庫存,提高資金效率,社會資源浪費會大大減少。
中國企業(yè)對精益管理的運用正處在起步階段,當前,推行精益管理模式中,需要明確以下幾個問題:
1、革新觀念,樹立精益意識。
中國有些企業(yè)過分強調擴大生產規(guī)模,在引進國外先進技術裝備時,片面追求高自動化和高生產效率,而不考慮整個生產過程和需求的均衡性,企業(yè)重技術輕管理現(xiàn)象也比較普遍。革新觀念,樹立精益意識,企業(yè)才能有救地遏制浪費,提高資金運用效率,增強競爭能力。
2、加強對精益思維的學習和研究。
精益思維是精益管理的核心。西方國家曾建立示范中心,推廣精益管理。中國許多企業(yè)對精益管理比較陌生,政府和社會應積極引導企業(yè),鼓勵企業(yè)運用精益管理方法,建立精益企業(yè)研究中心和示范中心,舉辦培訓研討班,灌輸精益管理,讓企業(yè)結合自身情況,按照精益思維原理進行改進和改造活動。
3、推行精益管理模式應循序漸進。
精益管理不是企業(yè)管理活動的全部,它應與企業(yè)的其它管理活動相協(xié)調,同時,不同行業(yè)不同企業(yè)的客觀環(huán)境不一樣,企業(yè)管理適宜方法也不一致。精益管理只是生產管理的一種較好模式,具體實施要因地制宜。只有每一個企業(yè)都有自己的“精益原則”,這才真正得到了精益管理的精髓。
精益生產管理推行有哪些價值?以上就是新益為精益生產咨詢公司的相關介紹,做好企業(yè)的生產管理工作就是為精益生產管理活動打下基礎,讓精益生產管理在企業(yè)中發(fā)展有一個良好的前提。
建立生產有序、管理順暢,操作規(guī)范,士氣高昂、高質量、低成本、短交期的作業(yè)現(xiàn)場;
為企業(yè)規(guī)劃設計一套由內到外的形象升級,外觀視覺價值體現(xiàn)、內在的管理內涵體現(xiàn);
全員參與設備管理高產出和低成本運營,提升設備管理能力,維護能力,提高效率
構建班組生產管理體系、循環(huán)評價、人才育成、持續(xù)改善、績效管理、文化養(yǎng)成體系;
提高產品質量、降低生產成本、縮短交期、增加利潤,讓管理更系統(tǒng)科學,執(zhí)行力更強
對工廠的各個組成部分進行合理安排,以提高生產效率、降低成本、優(yōu)化物流、改善工作環(huán)境等